روانکاري علم تسهيل حرکت نسبي سطوح در تماس با يکديگر است. اين علم بهعنوان يکي از رشتههاي بسيار مهم در علوم مهندسي شناخته ميشود، بهطوريکه موفقيت بسياري از طرحهاي صنعتي در گرو آگاهي از اين دانش فني خواهد بود. امروزه توسعه صنعت روانکار يک بخش مهم از توسعه صنايع ماشيني و صنايع مربوط به آن شدهاست. علاوهبراين، با مطرحشدن بحثهاي جديدي چون بهينهسازي مصرف و حفظ منابع تجديدناپذير و همچنين رعايت الزامات زيستمحيطي، مطالعه بر روي روانکارها جايگاه خاصي در بين علوم پيدا کردهاست.
براي جلوگيري از فرسايش و از کارافتادگي زودرس ماشينآلات صنعتي و همچنين دسترسي به بيشترين بازده مکانيکي در حداقل زمان يک برنامه روانکاري مناسب جزء مهمترين شرايط مورد نياز خواهد بود. در قرن حاضر برنامه روانکاري مناسب، يک برنامه روانکاري پايدار است که شايد کمي با تعاريف روانکاري قديمي متفاوت باشد.
نوع روانکار، مقدار، زمان و مکان مناسب، چهار عامل مهم در عمل روانکاري هستند که امروزه براي يک روانکاري موفق علاوه بر آنها بايد هزينههاي نگهداري، تعميرات، عمليات (هزينه سوخت، استهلاک و ...) و رعايت قوانين و الزامات زيستمحيطي را نيز درنظر گرفت. آمار نشان ميدهد تنها با يک افزايش 1 يا 2 درصدي در هزينه براي يک روانکاري بهتر ميتوان حدود 15% از هزينههاي اضافي يک خودرو را کاهش داد. ضمن اينکه استفاده از يک روانکار مناسب فاصله زماني تعويض روغن براي يک خودرو را زياد ميکند که اين مسئله به حفظ محيط زيست و در نهايت حفظ منابع تجديدناپذير نيز کمک ميکند و لذا اين مسئله خود بيانگر اهميت دانش فني روانکارهاست. درست است که در روانکاري علاوه بر کيفيت، هزينههاي مصرفي را نيز بايد در نظر گرفت اما شعار شرکتهاي بزرگ توليدکننده روانکار، انتخاب بهترين به جاي ارزانترين است. در اکثر موارد هزينهاي که بايد براي تعميرات قطعات مستهلک که ناشي از استفاده روانکار نامناسب است، بپردازيم بسيار بيشتر از هزينهاي است که ميتوانستيم براي يک روانکار گرانتر ولي بهتر در نظر بگيريم.
بهطور کلي به لايههاي گاز، مايع و يا جامد که ميان دو سطح قرار ميگيرند و يکنواختي حرکت يک سطح بر روي ديگري را بهبود ميبخشند و از ايجاد آسيب بر روي سطوح جلوگيري ميکنند، روانکار گويند.
علاوه بر کنترل و کاهش اصطکاک و سايش بين دو سطح که جزء وظايف اصلي يک روانکار است، يک روانکننده وظايف ديگري نيز دارد که عبارتند از:
روانکارها کاربردهای بسيار مهمي در موتورهاي احتراق داخلي، وسايل نقليه، چرخ دندههاي صنعتي، کمپرسورها، توربينها، سيستمهاي هيدروليک و ... دارند. 90% از روانکارهاي مصرفي را روغنهاي روانکار تشکيل ميدهند که در بين آنها روغنهاي خودرو بيشترين مصرف را دارند.
در حال حاضر بيش از 1700 توليدکننده روانکار در سراسر جهان وجود دارند که حدود 200 شرکت بهصورت جانبي و در کنار توليدات ديگر روانکار توليد ميکنند و حدود 1500 شرکت بهطور اختصاصي به توليد روانکار پرداختهاند. بيش از 60% از روانکارهاي مصرفي در سراسر دنيا توسط کمتر از 2% اين شرکتها توليد ميشود. در جدول 1-1 نام 16 شرکت از بزرگترين توليدکنندگان روانکارها در دنيا و در جدول 1-2 نيز نام بزرگترين توليدکنندگان روانکارهاي صنعتي آمدهاست.
جدول 1-1 بزرگترين توليدکنندگان روانکار جهان
جدول 1-2 بزرگترين توليدکنندگان روانکارهاي صنعتي جهان
تقسيمبندي انواع روانکارها
طرح شماتیک زیر تقسیم بندی انواع روانکارها بر حسب نوع کاربرد را نمایش می دهد.
همانطورکه مشاهده می کنید روانکارها را در يک نگاه کلي مي توان به دو دسته بزرگ روانکارهاي خودرو و روانکارهاي صنعتي تقسيم کرد. روانکارهاي صنعتي نيز به سه دسته عمده روغنهاي صنعتي، گریسها و روانکارهاي ویژه ديگر مثل روانکارهاي فلزکاري و ... تقسيم ميشوند.
البته روانکارها را از نظر نوع حالت نيز می توان طبقهبندي کرد. که به چهار دسته روانکنندههاي گازي، روانکنندههاي مايع، گريسها و روانکنندههاي جامد تقسيم ميشوند.
روانکارهاي گازي
روانکارهاي گازي مثل هوا، هليوم، بخار مايعات و ... در موارد درجه حرارتهاي خيلي بالا و يا پايين، سرعت بسيار زياد و بارکم و يا در مواردي که پرتوهاي هستهاي در محيط وجود دارند، استفاده ميشوند. يکي از خصوصيات بسيار مهم روانکارهاي گازي اينست که گرانروی آنها با تغيير درجه حرارت تغيير چنداني نميکند و به همين دليل اين روانکارها قادرند در گسترهی وسيعي از کاربردهاي صنعتي مورد استفاده قرار گيرند. علاوه بر اين چون گازها سبکتر از مايعات هستند و ميتوان وزن آنها را ناديده گرفت، اين موضوع باعث ميشود در سرعتهاي خيلي بالا همچنان جريان آنها آرام و يکنواخت باقي بماند. به همين جهت در ياتاقانهاي با سرعت خيلي زياد بهتر از روانکارهاي مايع عمل می کنند.
روانکارهاي گازي اصطکاک کمي دارند، عاري از ناخالصياند و خاصيت سرريزي که در مورد روانکارهاي مايع و گريسها پيش ميآيد را ندارند. علاوه بر آن اين نوع روانکارها بدليل سرريز نکردن ميتوانند مواد مطمئني در صنايع غذايي، داروئي و شيميايي نيز باشند.
روانکاري اولتراسانتريفيوژها، ماشينهاي ابزار سنگزني دقيق که با سرعت زياد کار ميکنند، چرخ مته دندانپزشکي، راکتورهاي اتمي، ماشينهاي ريسندگي پرسرعت، توربينهاي گازي، موتور جت و ... از جمله موارد کاربرد اين دسته از روانکارها هستند.
روانکارهاي مايع
مهمترين روانکارهاي مايع روغنها هستند که خود به دو دسته بزرگ روغنهاي معدني و روغنهاي سنتزي تقسيمبندي ميشوند. اين نوع روانکارها رايجترين و پرمصرفترين نوع روانکارها هستند. هر دو دسته به نوعي از مشتقات نفت خام به حساب ميآيند، با اين تفاوت که روغنهاي معدني از انجام يک سري عمليات تفکيک بر روي نفت خام و حداکثر يک واکنش شيميايي کنترل شده بهدست ميآيند درصورتيکه براي توليد روغنهاي سنتزي واکنشهاي شيميايي کنترل شده بيشتري مورد نياز است و به همين دليل قيمت تمام شده روغنهاي سنتزي بيشتر از روغنهاي معدني خواهد بود. بهطور کلي روغنهاي معدني بدليل کاربرد فراواني که در توليد روانکارها دارند نسبت به روغنهاي سنتزي، بيشتر توليد ميشوند. البته قابليتهاي يک روغن سنتزي بدليل واکنشهاي مخصوصي که روي آن انجام شده بيشتر از يک روغنپايه معدني است، زيرا روغنهاي کاملاً مناسب بهطور مصنوعي توليد شده و در طبيعت قابل کشف نيستند.
البته به جز روغنهاي سنتزي و روغنهايي که منبع اصلي آنها نفت خام است روغنهاي ديگري نيز وجود دارند که از جانوران، ماهيها و گياهان بهدست ميآيند که روغنهاي طبيعي نام دارند. استفاده از اين روغنها بهعنوان روانکار در گذشته بسيار مرسوم بوده است ولي امروزه نفت خام منبع اصلي توليد روانکارها است. يکي از خصوصيات روغنهای طبيعی تجزيه بيولوژيکي آسان آنها است که از اين لحاظ نسبت به روغنهاي پايه معدني و سنتزی برتري دارند. اين روغنها براي مدت طولاني قابل نگهداري نيستند، ضمن اينکه هزينهی توليد زيادي هم دارند. اما با توجه به محدود بودن منابع نفتي براي توليد انرژي، روغنهاي طبيعي ميتوانند جايگزين مناسبي براي مشتقات نفتي در عرصه توليد روانکار باشند.
گريسها
گريسها جزء معروفترين روانکارها هستند که نه مايع و نه جامدند. گريسها از يک روغنپايه معدني يا سنتزي و يک سفتکننده بهدست ميآيند. در مواردي که روانکاري با روانکارهاي مايع مشکل بوده و امکان روانکاري مجدد دارای محدوديت می باشد، اين نوع روانکارها کاربرد فراواني خواهند داشت.
روانکارهاي جامد
اين نوع روانکارها براي کار در شرايط بخصوص مثل خلاء، بار زياد و يا حرارت بالا و مكانهايي مثل راکتورهاي هستهاي که در برابر اشعههاي راديواکتيو قرار دارند استفاده ميشوند.
مقاوم بودن در حالت خلا، فراريت کم، درجهحرارتهاي بالا و همچنين در برابر انرژيهاي ناشي از تابش مواد راديواکتيو از مهمترين خواص يک روانکار است و روانکارهاي جامد داراي اين خصوصيات هستند.
گرافيت، موليبونيوم ديسولفيد، بورنيتريد، تنگستن ديسولفيد و برخي ترکيبات آلي جامد مثل فتالوسيانين و تترافلوئورواتيلن، ميکا، تالك و ... از انواع روانکارهاي جامد هستند که در اين بين گرافيت و موليبونيوم ديسولفيد، بيشترين کاربرد را دارند.
براي جلوگيري از فرسايش و از کارافتادگي زودرس ماشينآلات صنعتي و همچنين دسترسي به بيشترين بازده مکانيکي در حداقل زمان يک برنامه روانکاري مناسب جزء مهمترين شرايط مورد نياز خواهد بود. در قرن حاضر برنامه روانکاري مناسب، يک برنامه روانکاري پايدار است که شايد کمي با تعاريف روانکاري قديمي متفاوت باشد.
نوع روانکار، مقدار، زمان و مکان مناسب، چهار عامل مهم در عمل روانکاري هستند که امروزه براي يک روانکاري موفق علاوه بر آنها بايد هزينههاي نگهداري، تعميرات، عمليات (هزينه سوخت، استهلاک و ...) و رعايت قوانين و الزامات زيستمحيطي را نيز درنظر گرفت. آمار نشان ميدهد تنها با يک افزايش 1 يا 2 درصدي در هزينه براي يک روانکاري بهتر ميتوان حدود 15% از هزينههاي اضافي يک خودرو را کاهش داد. ضمن اينکه استفاده از يک روانکار مناسب فاصله زماني تعويض روغن براي يک خودرو را زياد ميکند که اين مسئله به حفظ محيط زيست و در نهايت حفظ منابع تجديدناپذير نيز کمک ميکند و لذا اين مسئله خود بيانگر اهميت دانش فني روانکارهاست. درست است که در روانکاري علاوه بر کيفيت، هزينههاي مصرفي را نيز بايد در نظر گرفت اما شعار شرکتهاي بزرگ توليدکننده روانکار، انتخاب بهترين به جاي ارزانترين است. در اکثر موارد هزينهاي که بايد براي تعميرات قطعات مستهلک که ناشي از استفاده روانکار نامناسب است، بپردازيم بسيار بيشتر از هزينهاي است که ميتوانستيم براي يک روانکار گرانتر ولي بهتر در نظر بگيريم.
بهطور کلي به لايههاي گاز، مايع و يا جامد که ميان دو سطح قرار ميگيرند و يکنواختي حرکت يک سطح بر روي ديگري را بهبود ميبخشند و از ايجاد آسيب بر روي سطوح جلوگيري ميکنند، روانکار گويند.
علاوه بر کنترل و کاهش اصطکاک و سايش بين دو سطح که جزء وظايف اصلي يک روانکار است، يک روانکننده وظايف ديگري نيز دارد که عبارتند از:
- جلوگيري از خوردگي و زنگزدگي سطح فلزات
- پاککنندگي سطوح و تعليق ذرات ناخالص و جلوگيري از رسوب آنها بر روي قطعات سيستم
- انتقال قدرت و انرژي هيدروليکي
- آببندي سيستم و ...
روانکارها کاربردهای بسيار مهمي در موتورهاي احتراق داخلي، وسايل نقليه، چرخ دندههاي صنعتي، کمپرسورها، توربينها، سيستمهاي هيدروليک و ... دارند. 90% از روانکارهاي مصرفي را روغنهاي روانکار تشکيل ميدهند که در بين آنها روغنهاي خودرو بيشترين مصرف را دارند.
در حال حاضر بيش از 1700 توليدکننده روانکار در سراسر جهان وجود دارند که حدود 200 شرکت بهصورت جانبي و در کنار توليدات ديگر روانکار توليد ميکنند و حدود 1500 شرکت بهطور اختصاصي به توليد روانکار پرداختهاند. بيش از 60% از روانکارهاي مصرفي در سراسر دنيا توسط کمتر از 2% اين شرکتها توليد ميشود. در جدول 1-1 نام 16 شرکت از بزرگترين توليدکنندگان روانکارها در دنيا و در جدول 1-2 نيز نام بزرگترين توليدکنندگان روانکارهاي صنعتي آمدهاست.
جدول 1-1 بزرگترين توليدکنندگان روانکار جهان
نام کشور | نام شرکت |
آمريکا | Exxon Mobil |
بريتانيا/ هلند | Shell |
آمريکا | Chevron Texaco Caltex |
انگليس | BP CASTROL |
چين | Sinopec / Cnpc |
آمريکا | Pennzoil Quaker State |
فرانسه | Total Fina Elf |
ژاپن | Nippon Mitsubishi Oil / Fuji Kasan / Koa oil |
روسيه | Lukoil |
آمريکا | Valvoline |
آمريکا | Sun |
ژاپن | Idemitsu |
آلمان | Fuchs |
هند | Indian Oil |
ايتاليا | Agip/ Petrogai |
اسپانيا | Repsol - YPF |
جدول 1-2 بزرگترين توليدکنندگان روانکارهاي صنعتي جهان
نام کشور | نام شرکت |
آمريکا | Exxon Mobil |
بريتانيا / هلند | Shell |
چين | Sinopec / Cnpc |
آمريکا | Chevron Texaco Caltex |
انگليس | Bp CASTROL |
آلمان | Fuchs |
تقسيمبندي انواع روانکارها
طرح شماتیک زیر تقسیم بندی انواع روانکارها بر حسب نوع کاربرد را نمایش می دهد.
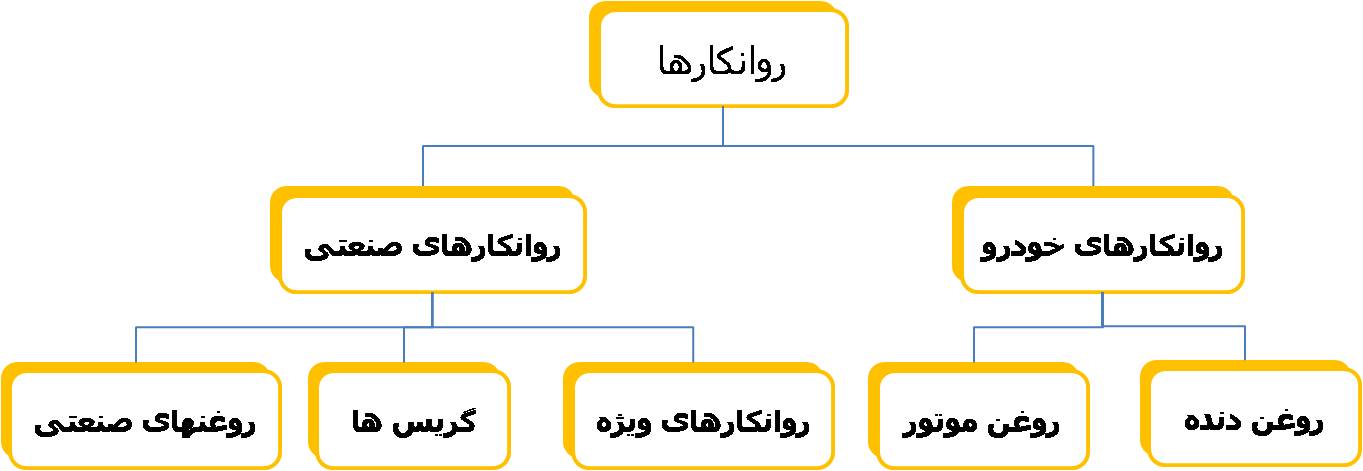
البته روانکارها را از نظر نوع حالت نيز می توان طبقهبندي کرد. که به چهار دسته روانکنندههاي گازي، روانکنندههاي مايع، گريسها و روانکنندههاي جامد تقسيم ميشوند.
روانکارهاي گازي
روانکارهاي گازي مثل هوا، هليوم، بخار مايعات و ... در موارد درجه حرارتهاي خيلي بالا و يا پايين، سرعت بسيار زياد و بارکم و يا در مواردي که پرتوهاي هستهاي در محيط وجود دارند، استفاده ميشوند. يکي از خصوصيات بسيار مهم روانکارهاي گازي اينست که گرانروی آنها با تغيير درجه حرارت تغيير چنداني نميکند و به همين دليل اين روانکارها قادرند در گسترهی وسيعي از کاربردهاي صنعتي مورد استفاده قرار گيرند. علاوه بر اين چون گازها سبکتر از مايعات هستند و ميتوان وزن آنها را ناديده گرفت، اين موضوع باعث ميشود در سرعتهاي خيلي بالا همچنان جريان آنها آرام و يکنواخت باقي بماند. به همين جهت در ياتاقانهاي با سرعت خيلي زياد بهتر از روانکارهاي مايع عمل می کنند.
روانکارهاي گازي اصطکاک کمي دارند، عاري از ناخالصياند و خاصيت سرريزي که در مورد روانکارهاي مايع و گريسها پيش ميآيد را ندارند. علاوه بر آن اين نوع روانکارها بدليل سرريز نکردن ميتوانند مواد مطمئني در صنايع غذايي، داروئي و شيميايي نيز باشند.
روانکاري اولتراسانتريفيوژها، ماشينهاي ابزار سنگزني دقيق که با سرعت زياد کار ميکنند، چرخ مته دندانپزشکي، راکتورهاي اتمي، ماشينهاي ريسندگي پرسرعت، توربينهاي گازي، موتور جت و ... از جمله موارد کاربرد اين دسته از روانکارها هستند.
روانکارهاي مايع
مهمترين روانکارهاي مايع روغنها هستند که خود به دو دسته بزرگ روغنهاي معدني و روغنهاي سنتزي تقسيمبندي ميشوند. اين نوع روانکارها رايجترين و پرمصرفترين نوع روانکارها هستند. هر دو دسته به نوعي از مشتقات نفت خام به حساب ميآيند، با اين تفاوت که روغنهاي معدني از انجام يک سري عمليات تفکيک بر روي نفت خام و حداکثر يک واکنش شيميايي کنترل شده بهدست ميآيند درصورتيکه براي توليد روغنهاي سنتزي واکنشهاي شيميايي کنترل شده بيشتري مورد نياز است و به همين دليل قيمت تمام شده روغنهاي سنتزي بيشتر از روغنهاي معدني خواهد بود. بهطور کلي روغنهاي معدني بدليل کاربرد فراواني که در توليد روانکارها دارند نسبت به روغنهاي سنتزي، بيشتر توليد ميشوند. البته قابليتهاي يک روغن سنتزي بدليل واکنشهاي مخصوصي که روي آن انجام شده بيشتر از يک روغنپايه معدني است، زيرا روغنهاي کاملاً مناسب بهطور مصنوعي توليد شده و در طبيعت قابل کشف نيستند.
البته به جز روغنهاي سنتزي و روغنهايي که منبع اصلي آنها نفت خام است روغنهاي ديگري نيز وجود دارند که از جانوران، ماهيها و گياهان بهدست ميآيند که روغنهاي طبيعي نام دارند. استفاده از اين روغنها بهعنوان روانکار در گذشته بسيار مرسوم بوده است ولي امروزه نفت خام منبع اصلي توليد روانکارها است. يکي از خصوصيات روغنهای طبيعی تجزيه بيولوژيکي آسان آنها است که از اين لحاظ نسبت به روغنهاي پايه معدني و سنتزی برتري دارند. اين روغنها براي مدت طولاني قابل نگهداري نيستند، ضمن اينکه هزينهی توليد زيادي هم دارند. اما با توجه به محدود بودن منابع نفتي براي توليد انرژي، روغنهاي طبيعي ميتوانند جايگزين مناسبي براي مشتقات نفتي در عرصه توليد روانکار باشند.
گريسها
گريسها جزء معروفترين روانکارها هستند که نه مايع و نه جامدند. گريسها از يک روغنپايه معدني يا سنتزي و يک سفتکننده بهدست ميآيند. در مواردي که روانکاري با روانکارهاي مايع مشکل بوده و امکان روانکاري مجدد دارای محدوديت می باشد، اين نوع روانکارها کاربرد فراواني خواهند داشت.
روانکارهاي جامد
اين نوع روانکارها براي کار در شرايط بخصوص مثل خلاء، بار زياد و يا حرارت بالا و مكانهايي مثل راکتورهاي هستهاي که در برابر اشعههاي راديواکتيو قرار دارند استفاده ميشوند.
مقاوم بودن در حالت خلا، فراريت کم، درجهحرارتهاي بالا و همچنين در برابر انرژيهاي ناشي از تابش مواد راديواکتيو از مهمترين خواص يک روانکار است و روانکارهاي جامد داراي اين خصوصيات هستند.
گرافيت، موليبونيوم ديسولفيد، بورنيتريد، تنگستن ديسولفيد و برخي ترکيبات آلي جامد مثل فتالوسيانين و تترافلوئورواتيلن، ميکا، تالك و ... از انواع روانکارهاي جامد هستند که در اين بين گرافيت و موليبونيوم ديسولفيد، بيشترين کاربرد را دارند.